A South Wales company has developed an innovative way to recycle single use personal protective equipment (PPE) in a bid to tackle the mountain of waste being produced as a result of the pandemic.
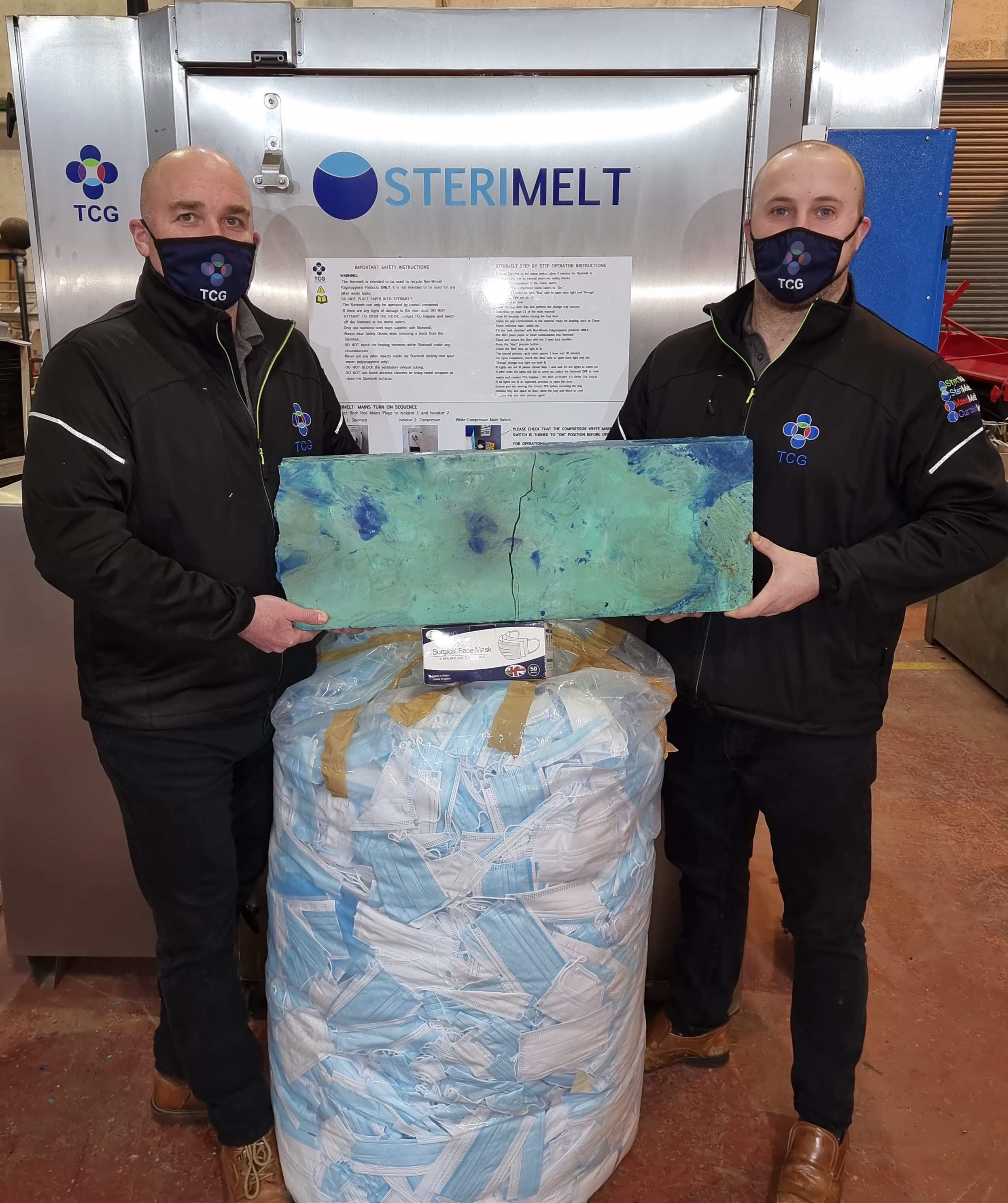
Cardiff-based Thermal Compaction Group (TCG) has become one of the first in the world to create a device to recycle disposable plastic PPE at source, which re-engineers an average 24 tonnes of polypropylene waste each year per unit. Following the outbreak, estimates suggest that hospital trusts across the UK have been using a combined 10million PPE items a day between them, the majority of which are single-use plastic, highlighting the scale of the problem.
The company is confident its patented ‘Sterimelt’ device, which thermally compacts polypropylene and re-engineers it so that it is suitable to make new products, will help curb this global challenge.
Initially developed to recycle polypropylene surgical tray wraps and drapes in hospitals, TCG has since adapted the machine to also recycle medical-grade surgical face masks and other types of PPE. The device works by heating polypropylene plastic up to 350°C in 20kg batches and then thermally compacting it into rectangular blocks that can be converted into pellets to make new plastic products.
TCG is now working closely with Hardshell, one of the UK’s first FFP3-grade mask-making facilities, also based in Cardiff, to test the product’s efficiency. The firm is currently trialling Hardshell’s disposable face coverings through its machine, using defective masks that would otherwise end up in landfill along with other used PPE. The collaboration means that TCG is helping to reduce waste even during the product’s development stage.
The company was introduced to Hardshell by Life Sciences Hub Wales, which works to accelerate the development and adoption of innovative solutions for better health and wellbeing.
TCG currently has its Sterimelt devices in seven hospital trusts across the UK, including the Aneurin Bevan University Health Board in Newport, which was the first adopter of the technology in 2016.
A further eight devices have been ordered by hospital trusts across the UK, which are being built for delivery by June with TCG already expecting further orders by the end of the year.
The blocks produced from the melting process are collected by TCG and sent onto its various collaborators such as Hull-based company, ReWorked, to create a range of new items, including bins. These products can be sent back to the hospital trusts to use as medical waste bins, creating a sustainable circular recycling chain.
As well as reducing single-use plastic waste, the innovative technology will significantly help trusts to reduce their carbon emissions by decreasing the volume of waste needing to be transported off-site. TCG estimates that for every 10,000 kilograms of waste put through Sterimelt, hospital trusts will save 7,500 kilograms of carbon emissions, equating to a 75% saving on their current output.
Thomas Davison-Sebry, Chief Sustainability Officer at Thermal Compaction Group, said:
“The Covid-19 pandemic has highlighted just how much waste is generated from disposable plastics and has also shown how unsustainable current waste management practices are on a global scale. The technologies and solutions that we’re working on will mean that single-use plastic does need not be single-use going forward.
“As well as using the blocks from the Sterimelt to make hospital bins, we’re working on developing the technology to be able to 3D print items such as arm casts and therefore reduce the gypsum waste that is now banned from landfill sites in the UK. The responses we’ve had from not only the UK, but across the world including Europe, Australia, New Zealand and the US has been phenomenal. We know the need for this technology is out there, so we’re excited to continue growing and supplying our machine internationally.”
While the Sterimelt device works for most polypropylene-based products, there are certain elements to a medical grade face mask that cannot be melted down such as the wired nose pieces. To help improve sustainability, TCG has been advising the companies it is working with, such as Hardshell, on making the PPE a single polymer material to enable the entire mask to be melted down in one go. The company has since been approached by many PPE manufacturers across the globe for help streamlining their products to ensure they are fully recyclable through TCG’s ‘at source’ solutions like Sterimelt.
Anil Kant, Chief Executive Officer at Hardshell, said:
“We are proud that we answered the call from the Welsh government to help Wales produce its own NHS certified surgical face masks, FFP2 and FFP3 respirators and we are incredibly excited to assist TCG develop this game changing technology. We are all mindful of the pressures on the environment with waste disposal, so we are thrilled with the opportunity for our polypropylene to avoid this fate and know it has a life beyond landfill.”
Commenting on the global success and innovation of the TCG, Cari-Anne Quinn, CEO, Life Sciences Hub Wales, said:
“The technology created by TCG is ground-breaking, and we’re proud to share another example of the brilliant innovation and dedication we are seeing from the life sciences industry in Wales.
“The global response to this made-in-Wales technology is incredible, and we hope to see TCG continue to grow and innovate new solutions to combat the mass waste generated from pandemic and tackle the ongoing environmental crisis.”
The Welsh Government has worked with more than 300 businesses throughout Wales to produce important supplies to respond to coronavirus since the First Minister’s call to action last year. This has included manufacturing PPE, hand sanitiser and ventilators right here in Wales.
In addition, the Welsh Government has worked hard to safely transport supplies and equipment needed from abroad and provided crucial support to companies through the SMART Cymru COVID-19 Research, Development and Innovation Fund to quickly develop much-needed supplies.
Tell us about your innovation
If you have an innovative project or idea and are looking to elevate your work programme, tell us more about it via our Innovation Enquiry Form.